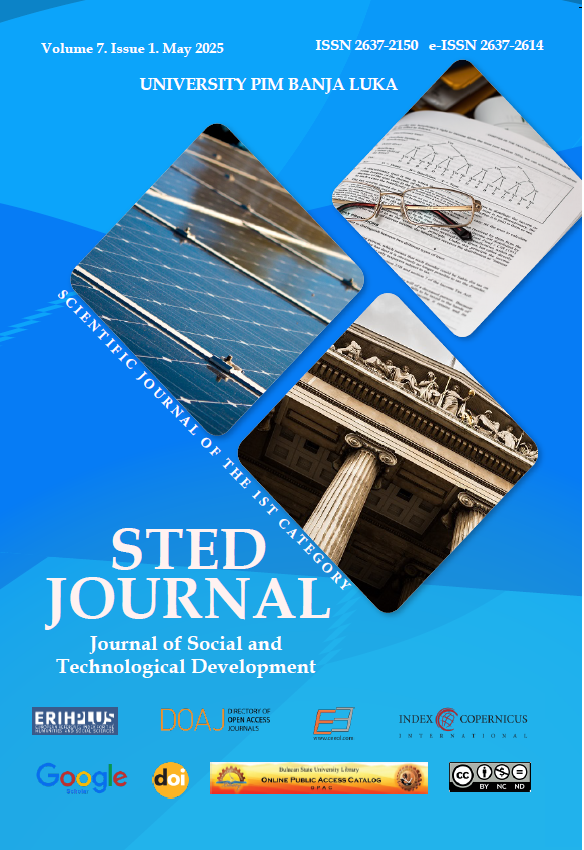
More articles from Volume 2, Issue 2, 2020
CONDUCTOMETRIC STUDY OF LIGAND STRUCTURE INFLUENCE ON THE Pb(II) COMPLEXATION WITH CROWN ETHERS
MECHANICAL ANALYSIS OF THE ROTATING DRAWING MANDREL WITH SELECTED BEARINGS CONFIGURATION
APPLICATION OF THE CRITERION OF TECHNOLOGICAL DAMAGEABILITY IN MECHANICAL ENGINEERING
BASICS OF AUTOMATION OF PROFILING OF HIGH-EFFICIENT INSERTS OF THE TOOL FOR THREAD MACHINING
CYBER CRIME IN PAKISTAN; DETECTION AND PUNISHMENT MECHANISM
Article views
MECHANICAL ANALYSIS OF THE ROTATING DRAWING MANDREL WITH SELECTED BEARINGS CONFIGURATION
Faculty of Manufacturing Technologies with a seat in Presov, Technical University of Košice , Košice , Slovakia
Faculty of Manufacturing Technologies with a seat in Presov, Technical University of Košice , Košice , Slovakia
Faculty of Manufacturing Technologies with a seat in Presov, Technical University of Košice , Košice , Slovakia
Institute of Geonics, The Czech Academy of Sciences , Poruba, Czech Republic
Faculty of Manufacturing Technologies with a seat in Presov, Technical University of Košice , Košice , Slovakia
Received: 20.10.2020.
Accepted: 20.11.2020. >>
Published: 30.11.2020.
Volume 2, Issue 2 (2020)
pp. 9-12;
Abstract
Nowadays is important to increase power efficiency in the heat production sector. Tubes with shaped internal surface are one of the possibilities to improve efficiency of heat exchangers. In the fact of this is actual to look on the improvements of the process of forming from the perspective of the tool construction. Presented article is focused on mechanical analysis of the rotating mandrel for cold forming of tubes with shaped internal surface. As a proposed material of the tool was selected heat-treated tool steel. Analyses were performed with selected configuration of the bearings. One bearing was configured as radial and second bearing was configured as radial-axial. A result shows stresses in the mandrel and deformation of the mandrel under a load of forming pressure. Obtained results have potential to enhance knowledge in the area of construction of the forming tools.
Keywords
References
Citation
Copyright
All papers are licensed under a Creative Commons Attribution 4.0 International License.
Article metrics
The statements, opinions and data contained in the journal are solely those of the individual authors and contributors and not of the publisher and the editor(s). We stay neutral with regard to jurisdictional claims in published maps and institutional affiliations.