Current issue
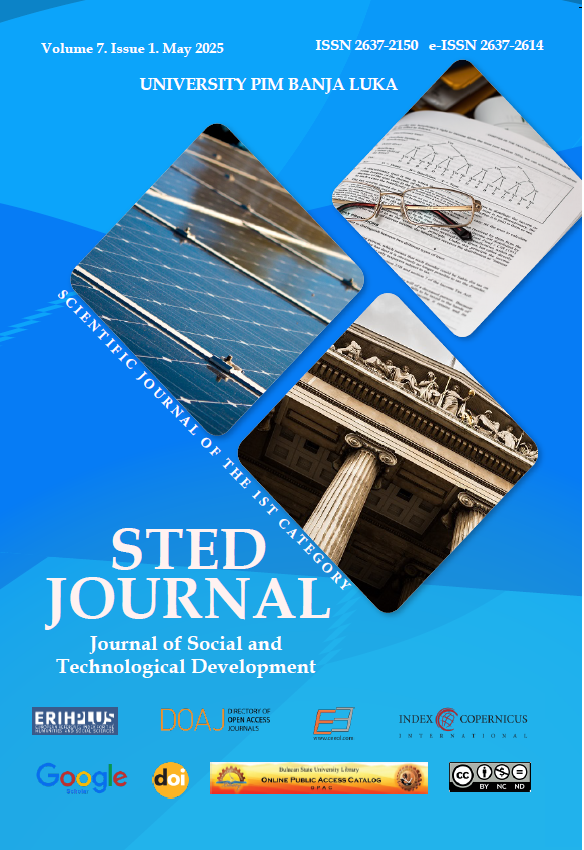
Volume 7, Issue 1, 2025
Online ISSN: 2637-2614
ISSN: 2637-2150
Volume 7 , Issue 1, (2025)
Published: 30.05.2025.
Open Access
All issues
Contents
30.11.2020.
Original scientific paper
BASICS OF AUTOMATION OF PROFILING OF HIGH-EFFICIENT INSERTS OF THE TOOL FOR THREAD MACHINING
Many modern threaded joints especially in the oil and gas industry, must satisfy high requirements for steel mechanical properties of which they are made. To ensure efficient threading of such hard-to-machine materials (ultimate strength is more than 1250 MPa), it is necessary to use carbide cutting inserts with the negative rake angle at its corner. However, modern manufacturers of such inserts make them only with a zero value of the rake angle. This is due to the difficulty of profiling of the insert cutting edge. This article proposes the basics of such inserts automatic profiling which is based on the algorithm developed by the authors. It includes two corrective calculations of the insert cutting edge profile, namely: the radial displacement of the corner and the tangential displacement of the area forming the crest of the thread. As a result, the computer application with the input parameter of the rake angle and output parameter of the upgraded profile of the insert cutting edge is received.
Oleh Onysko, Tetiana Lukan, Lolita Pituley, Iryna Shuliar, Yurii Havryliv
30.11.2020.
Original scientific paper
APPLICATION OF THE CRITERION OF TECHNOLOGICAL DAMAGEABILITY IN MECHANICAL ENGINEERING
Development and implementation in mechanical engineering practice of integrated information systems for control of technological processes of manufacturing products is the main driver of economic growth of developed countries. The priority of modern engineering technology is to provide the specified operational characteristics of products in accordance with the accuracy parameters, set by designer and quality of surface layers in contrast to achieving the minimum technological cost with maximum performance for traditional approaches. Technological providing of the main operational characteristics of the product (bearing strength, wear resistance, fatigue strength, joint strength etc.) require a systematic approach, which consists in the investigation of real physical processes at submicroscopic, microscopic and macroscopic levels of research, and step- by-step tracking required parameters at all stages of the Product Life Cycle from the position of technological inheritability. It is proposed to use the method of LM-hardness to control the quality of the structure of the material from castings in the design of functionally-oriented processes. The magnitude of the technological damage of the product material serves as a criterion for optimization when choosing a variant of surface treatment of the casting. A method for providing experimental studies of castings of aluminium alloys has been developed. On the basis of the carried-out experimental researches the rational route of processing of surfaces of casting is chosen.
Yaroslav Kusyi, Аndrij Кuк, Oleh Onysko, Tetiana Lukan, Lolita Pituley, Iryna Shuliar, Yurii Havryliv